The food industry in particular must manage its use of electricity as energy prices rise. As a major user of global power, food production companies need to develop plans to limit GHG emissions. Future Bridge has assembled an overview of tips and tricks the industry can use to best manage its facility energy use.
1. Energy use monitoring
Before any sort of energy management plan can be established, the company must understand how its facilities consume electricity. Most modern buildings already have metering points, but it is vital to combine this data. If necessary, hire an energy expert to make sense of this information. Fans, pumps, and refrigerators are commonly the main sources of energy consumption. But to what extent? By understanding how a facility operates, companies can create an energy management plan. Long-term metering can have cumulative benefits, as different seasons have different requirements. Modern, AI-driven monitoring systems help businesses keep track of consumption and predict future energy use.
2. Automation
AI and automation can also be used outside of metering and measuring. An energy management system (EMS) can process the energy use of all facility machinery simultaneously. It can calculate what rate certain machinery should work at and adjust it to output needs. EMS can also manage the facilities grid. Should a generating station disconnect, it can select the most energy-efficient way to reintroduce power. Imagine an operator using a higher-energy setting on a machine for a one-time event. Furthermore, if the operator does not revert the setting, the machine could be using more energy than necessary in all subsequent shifts. An automated system could quickly locate and rectify this human error.
3. More efficient refrigeration
The food industry relies on refrigeration systems to keep its products fresh. It is also a major energy consumption point. Some studies suggest that refrigeration may be 70% of a food company’s power bill. Modern refrigeration units tend to be more energy efficient, so a comprehensive analysis of current equipment may be important. Variable speed drives (VSDs) can be installed to cut energy use without sacrificing output. VSDs can adjust how the machine runs, so, for example, compressors can run at a reduced capacity when the necessary temperature is reached. Case studies in VSD HVAC systems found energy savings of up to 50%. Refrigeration systems that use chilled water can also benefit from VSDs, which control their pumps and throttle energy use when the temperature is correct. It is worth noting that some VSD systems can be integrated with AI to further increase efficiency.
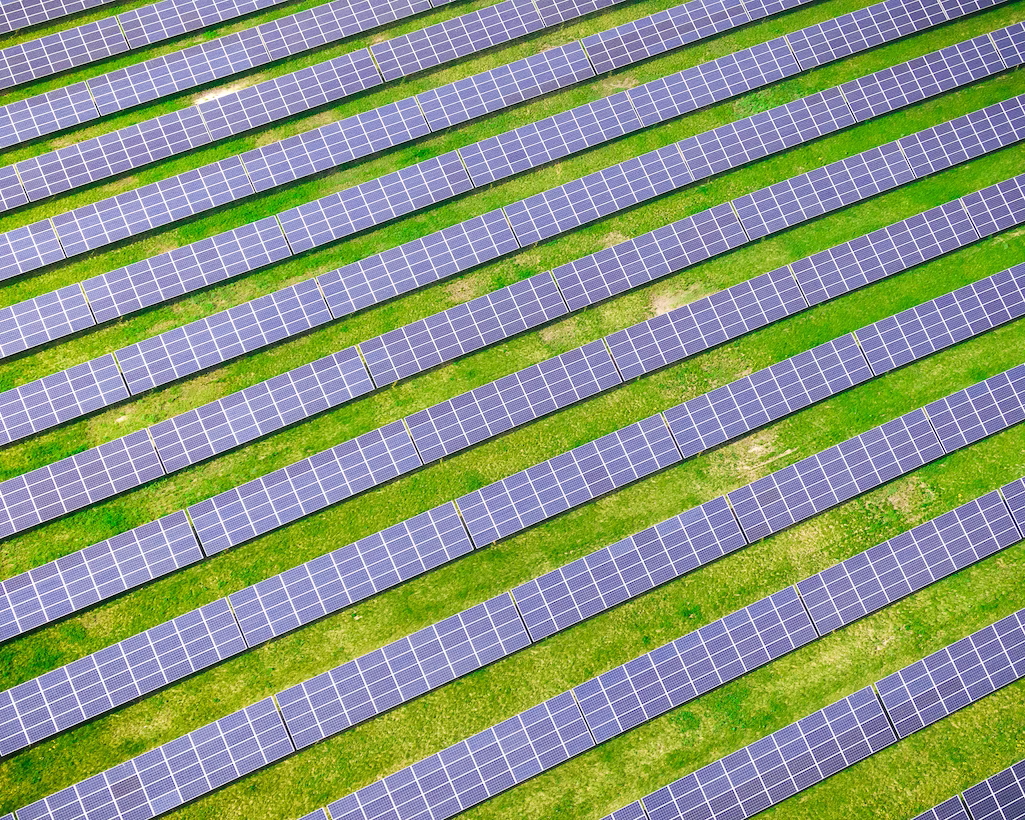
4. Green energy
Energy prices are rising and are likely to remain in flux. In the long term, companies may want to explore generating their own energy to power or partially power their facilities. Sunny areas are well disposed towards solar panels, while other locations can benefit from wind power. Certain industries already utilize renewable energy to help keep costs stable and controllable. For example, the Gudai-Darri mine in Australia produces 65% of its energy with solar panels. This has offset the mine’s CO2 emissions by 90,000tpa. Glencore’s Raglan mine in Canada utilizes wind energy in conjunction with a flywheel to store power for calmer days. This helps the operation cut emissions by 12,000 tonnes of CO2 that would otherwise be released from a diesel-operated mine. The food industry also has pioneers in the field of green energy. S Foods Singapore uses solar energy solutions as its main source of power for its Singapore facilities.
5. Green lighting
Similar to refrigeration, lighting is a major electricity sink. Modern LED systems are significantly more efficient than older bulbs and should be installed wherever possible. LED lamps and diodes have a predicted operational lifetime expectation of approximately 50,000 hours. Traditional lightbulbs are notoriously energy inefficient. Most of the power in a traditional bulb is lost through heat. LEDs do not suffer from this defect and turn most of the power supplied to them into the light. The lack of heat from an LED is particularly important in the food industry, which must maintain specific temperatures during production.
6. Reduce food waste
Between 10-20% of food produced never reaches the market and instead gets discarded. Wasted food has its own CO2 emissions, but more importantly, it still consumes the same amount of energy during production. Companies should investigate where in the production process is the majority of food lost. The aforementioned VSD systems have the potential to help, as they can regulate production speeds to match requirements and storage capacities.
Where should companies start?
The food industry needs to understand how to limit its energy consumption and by extension its CO2 emissions. Food production may use up to 30% of global energy and is increasingly under pressure from GHG emission regulations. Companies should make a holistic assessment of where new technology can be implemented. Industry peers are a valuable source of information, as learning from the experiences and mistakes of others is cheaper. Pitfalls to be avoided, case studies, and best practices should all be analyzed to make an informed energy management plan.
Companies need to learn from their peers who have embraced this technology. The Net Zero Food & Beverage Forum: Energy Efficiency and Decarbonisation conference, held from the 16th to 17th of February is an ideal opportunity. Industry leaders and innovators will gather in Berlin to discuss and exchange ideas and experiences with managing energy consumption. Visit future-bridge.eu or follow us on our social media to keep track of other events about energy use and decarbonisation.